
For instance, along the warp direction in a weaving process, continuous carbon fibre yarns can be used as the principal material while the recycled carbon fibre yarns can be used as a secondary material along the weft direction depending on the loading experienced by the structural component. They can still be used as a secondary material. However, from structural and strength point of view, these yarns are not recommended to be used as the principal reinforcing material in FRP composites. There are commercially available yarns produced from recycled short carbon fibre. Ĭonsidering the environmental impact, the technique presented in this study can be used to weave recycled carbon fibre yarns. Moreover, ORT woven composites have been successfully employed in the LEAP project to manufacture engine casings and fan blades for A-320-neo, 737-MAX and Comac C-919. The concept utilises the high thermal conductivity of ORT woven composites due to the through-thickness binding yarns creating a conduction path for the heat to dissipate. reported the use of ORT woven composite in ultra-light weight heat exchangers in the automotive industry. reported using ORT woven composites to replace high-strength steel beams. Not only LTL and AI woven composites have managed to find their way into industry, but also their ORT woven counterparts. 3D woven LTL composites have been utilised in the automotive industry.
#COMPOSITE PREFORM SKIN#
Applications in which continuous fibres are required for joining skin and stiffening elements as well managed to utilise those previously highlighted architectures, and consequently overcoming the need for bonding or fastening composite parts which is one of the major challenges facing 2D laminated composite nowadays. In addition, McClain reported successfully using 3Dwoven AI and LTL architectures in truss beams with integrated off-axis stiffeners. The main advantages observed for these architectures are that they have better interlaminar shear and radial stress resistance. In applications that require load transfer around a bend such as curved beams, T-joints and brackets, 3D woven AI and LTL architectures have been utilised. The applications of 3D woven composites have been growing tremendously in industry recently. Įxamples of possible weave binding patterns for ORT: (a) plain, (b) twill and (c) satin. The orthogonal interlock (ORT) ( Figure 1a) occurs when the interlacing angle between the binder and weft yarns is equal to 90°. The second category is a special case of the first one. The first category is the angle interlock (AI) in which the interlacing angle between the binder and weft yarns can have any value except 90° ( Figure 1c).

Then this classification is further divided according to the interlacing angle of the structure. If it penetrates all the way through the thickness it is referred to as through-thickness (TT) interlock (see Figure 1a, c) while it is classified as layer-to-layer (LTL) if the binder only holds adjacent layers (see Figure 1b). Generally, 3D woven composites can be divided into two main groups depending on how deep the binder penetrates through the fabric. For example one of the published studies entitled “Material Intensity of Advanced Composite Materials”, reported that the average figure for the electricity consumption is approximately 0.11 kWh per m 2 for glass fibres and 0.214 kWh/m 2 for carbon fibres. In terms of the energy consumption required for textile production, it depends very much on the type of the yarn and the weaving pattern. Although various techniques exist for manufacturing 3D textile preforms, the most widely used nowadays is weaving due to its high production rate along with the ability to produce various 3D woven structures. So, it reduces the manufacturing/machining cost and time even further. In addition, using textile technology can be utilised to manufacture near-net-shape preforms. The delamination resistance, due to the z-binder existence, enhances the impact performance and damage tolerance of such material systems. The “enhanced out-of-plane properties” is not the only advantage of 3D composites. This need requires replacing 2D laminated composites with three-dimensional (3D) textile structures. Thus, the need for composite materials with enhanced through-thickness “out-of-plane” properties has emerged. Wind turbine blades, stringers and stiffeners in aircraft, pressure vessels and construction applications are some examples of applications in which out-of-plane loading conditions are imposed on the structure.
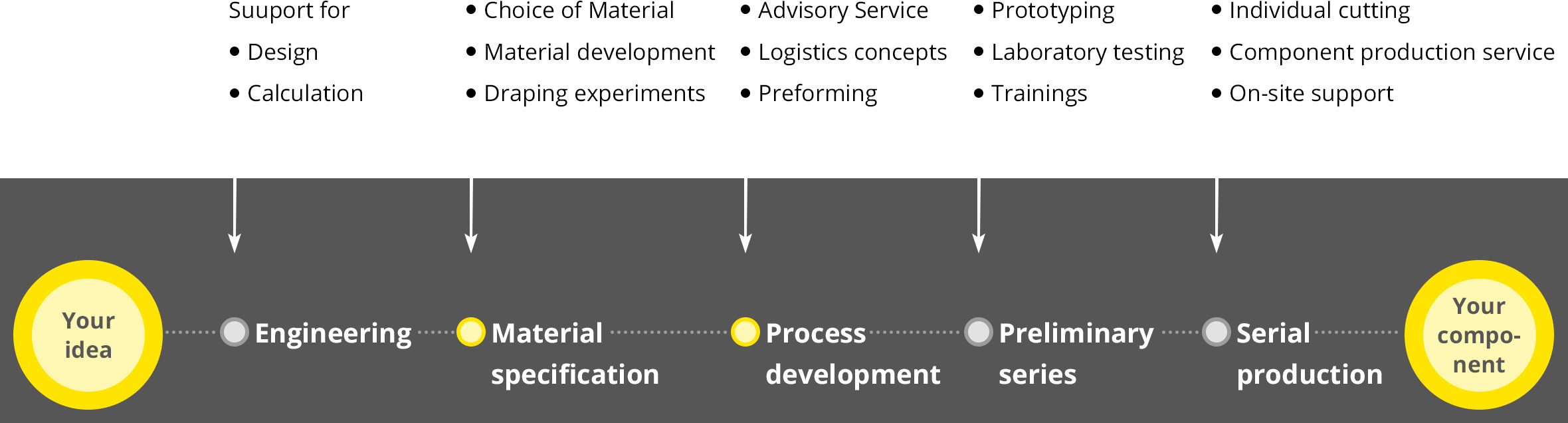
However, many real life applications are exposed to out-of-plane loading conditions that make it impossible to resort to the 2D laminates as the proper solution. Two-dimensional (2D) laminated composites are characterised by their in-plane high specific stiffness and strength.
